Access Denied
Sorry you are not allowed entry beyond this point.
To gain access to a vast World of Content is a simple task….
Existing Subscribers please login below. OR… Join Us for only £15 per year.!
If you are already a subscriber then please login below.
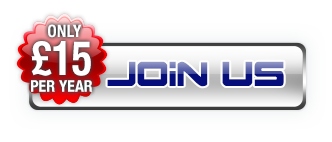